Philip Antunes, P.E., P.Eng.
INTRODUCTION
Colloidal mixers were developed in 1937 and are internationally recognized as the most efficient method of mixing cement based grouts (Houlsby, 1990). These mixers are used in grout preparation throughout the mining, tunnelling, heavy civil and general construction industries.
The key element of the colloidal mixer is the colloidal mill consisting of a high speed rotor (or discar) operating at 1700 rpm coupled with a close fitting chamber housing. The clearance between the discar and the walls of the housing is approximately 3 mm. It is here that a violent turbulence and high shearing action is created which is capable of breaking down clusters of dry cement particles (agglomerates).
The strong vortex action inside the tank rapidly assimilates the mix ingredients in as little as 2 minutes. The resultant slurry exhibits colloidal properties meaning the cement particles remain in suspension with minimal settling or bleed.
In combination, the high-speed shearing and the centrifugal actions of colloidal mixers thoroughly breaks up cement clumps and separates air bubbles, both of which slow the wetting process of cement grains. As a result, each grain is rapidly and thoroughly wetted and put into suspension.
The practical benefits of this combination include:
- The grout or slurry mix is nearly immiscible in water. This allows the mix to resist washout or contamination with groundwater.
- The mix is stable and fluid enough to allow it to be pumped considerable distances.
- The slurry permeates uniformly into voids.
- Segregation of sand, if incorporated in the mix, is virtually eliminated.
- The grout or slurry has less settlement (bleed) of the cement when stationary.
- Higher compressive strengths.
Of these benefits, the compressive strengths are perhaps the most notable due to the direct correlation to material savings and improved strengths. Numerous test results both in the lab and in the field show that colloidally mixed grouts produce higher strengths at all testing periods and densities when compared to paddle and non-colloidal mixers. In the figure below, the densities represent different water/cement ratios; as the cement content is increased, the density is correspondingly increased as well. While the figure represents a neat grout with only cement and water, it is important to note that this trend is also repeated for cellular and bi-component grouts. In fact, the colloidal technology produces consistently higher strengths in all types of grouts tested.
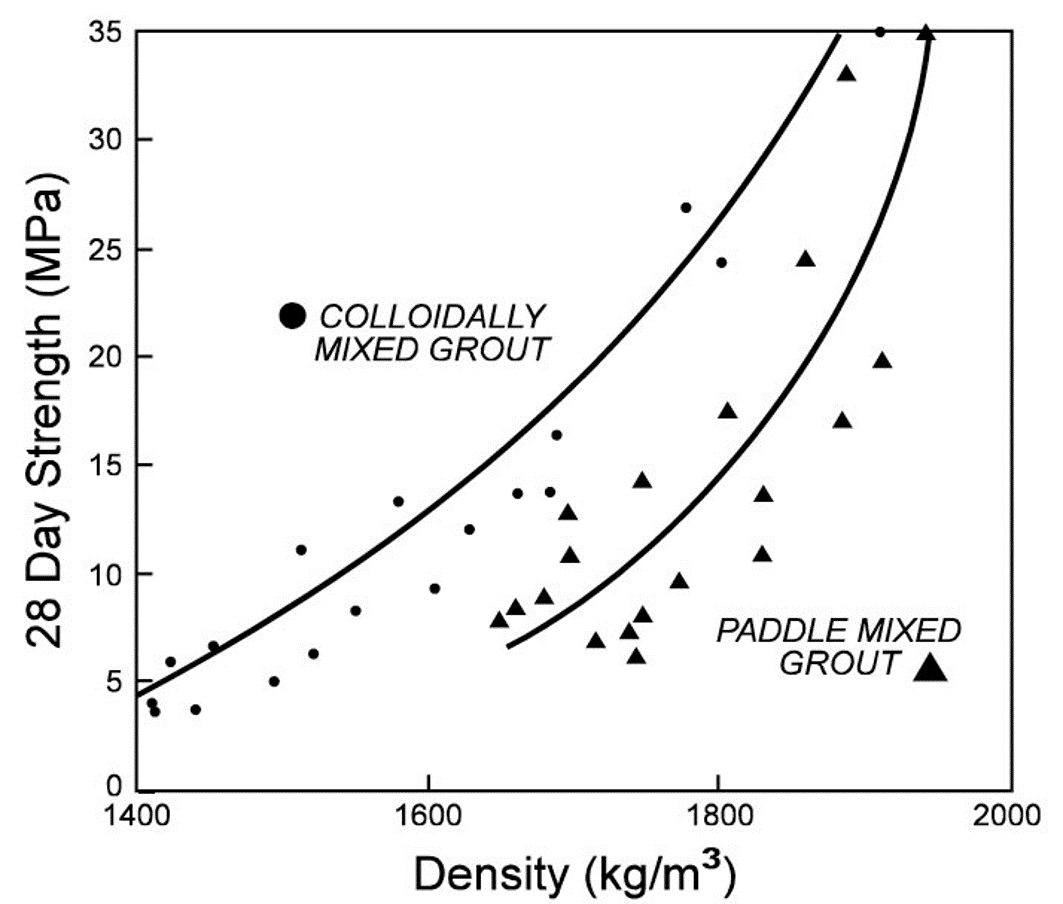
Figure 1: The 28-day strength of colloidal and paddle mixed grout