Originally published in ITA – AITES WTC 2016
Philip Antunes, P.E., P.Eng. – Team Mixing Technologies Inc.
A.E. (Tony) Reschke, M.Sc., P.Eng. – Team Mixing Technologies Inc.
INTRODUCTION
Tunnel Boring Machine (TBM) operations require the injection of material into the annular tail voids as the machine advances ahead of the segmental concrete lining. This annular gap is created because the cutting diameter of the TBM has to be larger than the outer diameter of the concrete segments of the tunnel lining.
Fundamentally, the two basic types of annular grout are thick, concrete like mortars and thin, mobile, two-component grouts. While some European countries seem to still favor the concrete like mortars, from a global perspective it is now the two-component type grouts that dominate the industry.
Two-component type grouts are comprised of an “A” component grout (typically cement, flyash, bentonite and a retarder/stabilizer) and a “B” component accelerator (sodium silicate or water glass as it is sometimes known). They are thus sometimes referred to as A/B type or bi-component grouts and were pioneered by the Japanese over 30 years ago. They offer a host of operational benefits over thick mortars, such as reduced settlement (Feddema et. al., 2001), effective penetration of the void space, with less energy, and reduced strain on the segmented linings (Robinson et. al., 2007). Two-component grouts are highly mobile and can be pumped many kilometers. The use of a retarder/stabilizer can also extend the shelf life of the “A” component grout for several days while the early strength of the accelerated grout stabilizes the ground and supports the segmental liner almost immediately.
The batch plants that prepare the two-component grouts use one of two possible mixing methods for preparing the “A” component grout. The simplest plants use paddle type mixers and numerous tunnels worldwide have been successfully grouted using this technology. However, a superior type of mixer is available, namely the high shear colloidal mixer.
Keller Colcrete successfully pioneered the development of the colloidal mixer back in 1937 and for over 75 years colloidal mixers have been internationally recognised as the most efficient method of mixing cement based grouts (Houlsby, 1990). These mixers are used in grout preparation for radioactive waste encapsulation, hydro dam grout curtains, soilcrete jet grouting, soil nailing, and numerous other geotechnical applications. In tunnelling, these mixers are also used for ground treatment, compensation grouting and for the preparation of bentonite lubrication for pipejacking. It has been only within the last decade however that these high-shear colloidal mixers have been adapted for use in the preparation of two-component grouts.
PRINCIPLES OF HIGH-SHEAR COLLOIDAL MIXING
Colloidal mixer design
While several brands of colloidal mixers are now available, the Colcrete type mixer design will be discussed below. Readers are referred to Houlsby (1990) for a more detailed design comparison of other commercially available colloidal and paddle type mixers.
Colloidal mill
The key element of the colloidal mixer is the colloidal mill (see Figure 1). The mill is comprised of a high speed rotor (or discar) operating at 2100 rpm coupled with a close fitting chamber housing. The discar is free to float horizontally on its mounting shaft with the internal fluid pressures centralising it in the housing. The clearance between the discar and the walls of the housing is approximately 3 mm. It is here that a violent turbulence and high shearing action is created which is capable of breaking down clusters of dry cement particles (agglomerates).
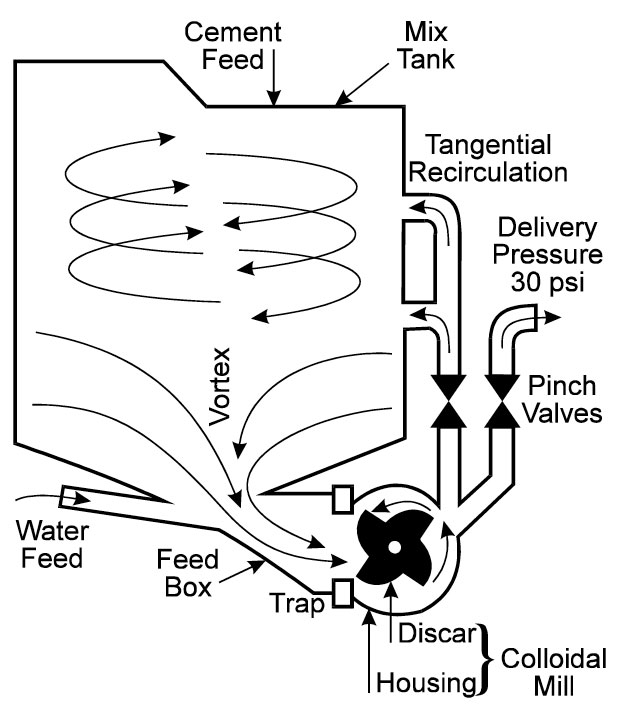
The colloidal mill also acts as a centrifugal pump. In a grout plant the colloidal mixer can thus directly discharge the mixed slurry into an agitation tank. The colloidal mill is capable of generating a maximum discharge pressure of 200 kPa. Depending on the batch size of the mixer, there may be up to 4 of these mills operating in unison each with a throughput of up to 750 l/min (200 USgpm).
It is possible to increase the mills efficiency as a pump (thus giving it a higher pressure capacity) but this would reduce its efficiency as a mixer. In fact, it is this lower pump efficiency that translates into more effective work being done on the material being mixed. There is simply more energy input into the mixing with the colloidal mixer. To illustrate this further, a 2000 litre colloidal mixer would have 4 x 22 kW motors (88 kW total) versus a 2000 litre paddle mixer which may have a single 15 kW mixing motor. More energy equates to better mixing.
The strong vortex action inside the tank rapidly assimilates the mix ingredients (cement, flyash, bentonite and admixtures) in as little as 2 minutes. The resultant slurry exhibits colloidal properties, i.e. the cement particles remain in suspension with minimal settling or bleed.
Mixing tank
The mixing tank, besides holding all the ingredients, also acts as a centrifugal separator. The centrifugal action of the circulating material spins the unmixed, thicker grout towards the outside of the tank whereas the lighter portions of the mix (the water and partly mixed grout) move inwards towards the throat of the tank and into the colloidal mill. Once through the mixer this lighter material is discharged tangentially into the outer part of the vortex, thus blending with the thicker, unmixed grout. Multiple passes through the rotor produce thicker and thicker grout until the entire mix becomes uniform and the centrifugal action can no longer separate differing densities. At this point the surface of the vortex has a smooth, uniform appearance.
The vortex action created inside the tank also helps to rapidly assimilate any admixtures into the mixer when first added. Depending on the size of the mixer the entire mixing process can take as little as 15 seconds.
Colloidal Suspensions
While the term ‘colloidal’ is often applied to high-shear mixers and the slurries they produce, strictly speaking, the term is incorrectly applied. ‘Semi-colloidal’ or ‘near-colloidal’ are more accurate descriptions. A colloid is defined as a solid, liquid, or gaseous substance made up of very small, insoluble, nondiffusible particles (as large molecules or masses of smaller molecules) that remain in suspension indefinitely in a surrounding solid, liquid, or gaseous medium of different matter. With cement based slurries, it is possible to filter out the solids (though perhaps not all if the cement is microfine) and individual grains can readily be seen. Particles will settle out leading to grout bleed. Cement slurries are thus not true colloidal suspensions.
The effect of the colloidal mixer, however, is to aggressively shear and break down individual cement grains and to make cement hydrates form of colloidal size such that the slurry exhibits colloidal properties, or in other words, forms a stable suspension.
Properties of high quality grouts and slurries
A high quality grout or slurry is regarded as having the following properties (Houlsby, 1990).
- Every particle of cement in the mix is thoroughly wetted. Individual grains are separate from each other without flocs or clumps.
- Each cement grain is surrounded by a film of water which chemically activates the particle, giving the full hydration necessary for strength and durability.
- The cement is thoroughly mixed with any other constituents of the mix or admixtures.
- The grout or slurry is uniform throughout.
- The mix exhibits some colloidal characteristics because of the maximum gel formation of the cement.
All of these properties can be attained with the use of high shear, high speed colloidal mixers. Kravetz (1959) explains that the high-speed shearing action combined with the centrifugal action of colloidal mixers thoroughly breaks up cement clumps and separates air bubbles, both of which slow the wetting process of cement grains. As a result, each grain is rapidly and thoroughly wetted and put into suspension. The mixing action also continually breaks away the hydrates that form on the surface of wetted cement grains exposing new areas to water. The hydrate elements that form are of colloidal size and as the amount of these elements increases the mixture becomes more colloidal in character.
Mayer (1959) measured the effect of high-shear colloidal mixing on cement grain size, particularly grains under 20 μm in size. The percentage of grains 5 μm in size was shown to be twice as large after high-speed mixing than with ordinary mixers, which accounted for the fact that the suspensions obtained were much more stable.
Practical benefits of colloidally mixed products
The practical benefits of colloidally mixed grouts and/or slurries include:
- The grout or slurry mix is nearly immiscible in water. This allows the mix to resist washout or contamination with groundwater.
- The mix is stable and fluid enough to allow it to be pumped considerable distances.
- The slurry permeates uniformly into voids.
- Segregation of sand, if incorporated in the mix, is virtually eliminated.
- The grout or slurry has less settlement (bleed) of the cement when stationary.
- Higher compressive strengths.
Colloidal mixers are clearly superior to paddle type mixers in the preparation of neat cement based slurries (Reschke, 1998) used in mining applications. As per Figure 2, higher strengths can be attained by virtue of the quality of the mixing of the cement and the water.
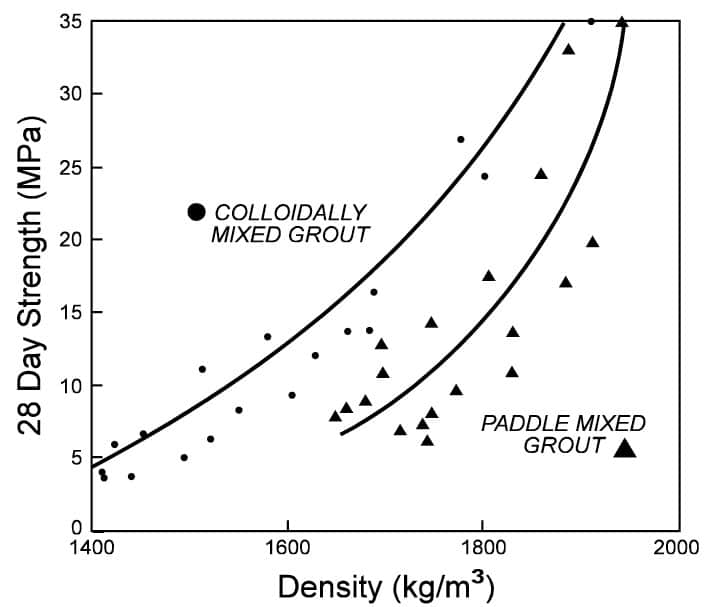
EFFECTS OF MIXING INTENSITY ON TWO COMPONENT GROUTS
Test Methods
To illustrate the benefits of using colloidal mixers in the preparation of two-component grouts comparative tests were conducted on a typical grout recipe (see Table 1) using a proprietary Team Mixing lab scale colloidal mixer, a model 130 Jiffler mixer in a ½” drill operating at 500 rpm, and a bench top Hobart HL120 mixer with paddles.
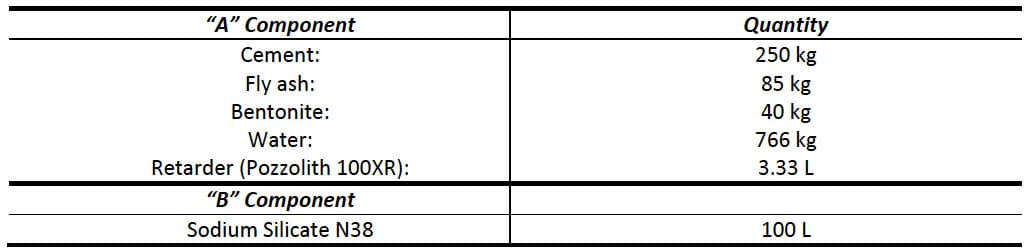
There are several key properties of two-component annular grouts that need to be considered in order for the stabilized and then accelerated grout to be effective. These include:
- Viscosity – critical to pumping requirements and the flow of grout in the annular gap.
- Bleed – critical to stability of grout in the pipeline.
- Gel time – need rapid gelling to lock segments in place
- Compressive strength – to support weigh of backup gantry bogey wheels.
All properties were tested in general accordance with ASTM standard procedures. Flowability was measured using a flow cone as per ASTM C939 specifications. Newtonian viscosity was measured directly from a Fann Model 35 Viscometer. Bleed was measured in graduated cylinders as per ASTM C940. Gel time was measured by mixing the grout and accelerator in a bucket and pouring the contents from one bucket to another until the grout will not flow any more. For early age compressive strength (<24 hrs or 1.5MPa) samples were tested using a constant strain rate loading frame as per ASTM D2166. For higher strength testing (>24 hr or 1.5MPa) then a constant load rate testing frame was used following C109 procedures. Readers are referred to Antunes (2012), for specific details on test methods and recommended deviations from ASTM standards to suit the particular properties of two-component grouts.
Test Results
Table 2 summarizes the average test results and, based on the authors experience, compares these to the desired range of properties required for the successful use of two-component grouts in tunneling.
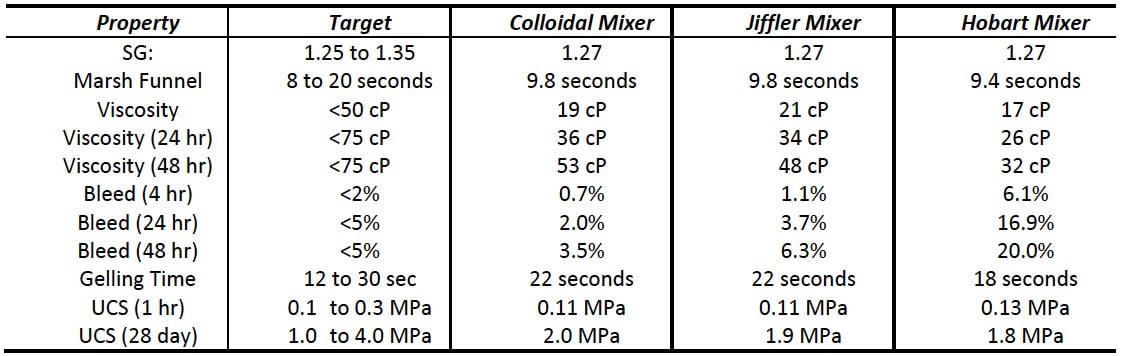
Viscosity
If the two-component grout is to be pumped from the surface batch plant to the TBM then flowability and viscosity are particularly important in determining pipeline specifications and surface pump pressures. A lower viscosity is preferred as it results in lower pipeline and pump pressures as well as lower power consumption. This becomes increasingly important the longer the conveyance pipeline gets. Test results indicate that the high shearing action of the colloidal and Jiffler mixers yield similar results. Interestingly the low intensity Hobart mixer actually yields lower viscosities. However, this is a result of the poor mixing action being unable to adequately break down the cement agglomerates and to disperse the bentonite particles (which causes gelling in the grout). Clumps of bentonite were visible in the Hobart mixed grout whereas the colloidal and Jiffler mixed grouts were homogenous in appearance.
Bleed
As with the discussion above on viscosities, grout bleed is an important consideration when pumping the grout to the TBM. Bleed within the grout results in settling of the cement particles along the invert of the pipeline. Severe bleed eventually leads to a constriction in the pipeline which requires higher and higher pump pressures to overcome. Regular cleaning of the lines with “pigs” can alleviate this problem to a point, particularly in lines less than 3,000 m. However, it is much more desirable to minimize the bleed from the onset. As contractors give serious consideration to pumping up to 9,000 m without any booster pumps in the tunnel, bleed becomes an absolutely critical parameter. The paddle type Hobart mixer simply does not provide adequate shearing action to disperse the bentonite. Consequently, the levels of bleed are unacceptable and not conducive to successful long distance pumping.
Gel Time
Generally speaking, longer gel times are more desirable as the single most common issue with the use of two-component grouts is blockages within the injection lines and ports after the accelerator is introduced. Longer gel times give adequate time for the accelerated grout to move from the injection lines out into the annular gap. Based on the test results the higher shear mixers give slightly longer gel times and are thus preferred.
Unconfined Compressive Strength (UCS)
The most common performance specification for the grout, given by designers and contractors, is an early compressive strength requirement. Early strengths are needed to ensure the segments do not sink within the annulus once internally loaded by the TBM backup gantry and to ensure adequate load transfer between the segmental lining and the soil. It is thus one of the most important performance parameters to consider.
All mixers tested gave adequate results for the 1 hr compressive strength. The Hobart mixer actually showed marginally better results but again this can be attributed to the poor dispersion of bentonite as bentonite is known to reduce the strengths of cement based grouts. The highest 28 day strengths were achieved with the colloidal mixer however the Jiffler mixer closely approximates the mixing quality of the colloidal mixer and appears to be a suitable lad mixer for simulating a high shear colloidal mixer.
Field Results
Figure 3 shows the field results achieved for grout strengths on the Airport Link Project in Brisbane (Reschke et al., 2011). The average results are shown (red dots) and compared to the initial lab results (open circles) which were conducted with a Hobart mixer for the same recipe. Once again we see significantly higher strengths attained from the use of a high shear colloidal mixer versus a low intensity paddle type mixer. For this particular grout recipe, the colloidally mixed grout had almost double the strength of the paddle mixed lab result used to determine the recipe for the project. The field results were so impressive that eventually the cement content in the grout was reduced by 7%. This resulted in a substantial cost savings to the contractor. Even with this cement reduction the strength performance still exceeded the minimum contractual requirement. Further reductions in cement content were therefore possible. The contractor however did not want to add any risk to the grouting program as this was the largest diameter TBM ever used in Australia at that time, and consequently, further optimization of the grout recipe was not pursued.
Similar strength gains were also encountered on the recently completed Istanbul Strait Road Tube Crossing Project under the Bosphorus. The two-component grout recipe was predetermined by lab testing with a paddle type mixer. In the field however, cement usage was actually reduced by 10% through the use of a colloidal mixer based batch plant (Gönenς, 2015).

Also shown in Figure 3 are field results for a paddle mixer based batch plant used on the Sydney Desalination Project (the circles with the cross). The grout mix recipe used here was virtually identical to the original Airport Link Project recipe. It can be seen that the grout strengths achieved in the field using a batch plant with a paddle mixer coincide extremely well with the lab test results using a paddle type Hobart mixer. This implies that the Hobart mixer is a useful lab tool that gives realistic results for field scale paddle mixer type style batching plants.
CONCLUSIONS
Both lab and field results have demonstrated the superior mixing capabilities of a high shear colloidal mixer versus a paddle type mixer. Higher strengths and lower bleeds result from the more energy intensive mixing action. As a result, the cement content in the “A” component grout can be reduced by up to 10% resulting in significant cost savings for the contractor. Lower bleed is also a critically important parameter to take into consideration if long (>3,000 m) pump distances are considered for a project.
Recent testing has also confirmed that the Hobart type paddle mixers are accurate for predicting field results of paddle mixer based grout batching plants. Conversely, the Jiffler style of lab mixer is better suited to predict the field properties of a colloidal mixer based grout plant.
REFERENCES
Antunes, P.F. 2012. Early Age Testing Procedure of Two-Component Annulus Grouts. In North American Tunnelling Convention 2012 Proceedings. Englewood, CO: Society for Mining, Metallurgy and Explorations, Inc. pp. 14-22.
Houlsby, A.C. 1990. Construction and Design of Cement Grouting – A Guide to Grouting in Rock Foundations. New York, NY: John Wiley & Sons. pp. 10-28.
Feddema, A., Moller, M., van der Zon, W.H. and Hasimoto, T. 2001. ETAC Two-Component Grout Field Test at Botlek Rail Tunnel. In Modern Tunnelling Science and Technology. Kyoto, Japan.
Gönenς, Ö. 2015. Personal communication, April.
Kravetz, G.A. 1959. Cement and Clay Grouting of Foundations: The Use of Clay in Pressure Grouting. ASCE Journal of Soil Mechanics and Foundation Division. New York, NY: American Society of Civil Engineers. pp. 109-114.
Mayer, A, 1959. Cement and clay grouting of foundations: French grouting practice, ASCE Journal of Soil Mechanics and Foundation Division. New York, NY: American Society of Civil Engineers. pp. 41.
Reschke, A.E. 1998. The Development of Colloidal Mixer Based CRF Systems. In MINEFILL 98, Edited by Dr. M. Bloss. Carlton, Australia: Australian Institute of Mining and Metallurgy. pp. 65-70.
Reschke, A.E. and Noppenberger, C. 2011. Brisbane Airport Link Earth Pressure Balance Machine Two Component Tailskin Grouting – A New Australian Record. In 14th Australasian Tunnelling Conference 2011. Carlton, Australia. Australian Institute of Mining and Metallurgy. pp. 609-617.
Robinson, B. and Bragard, C. 2007. Los Angeles Metro Gold Line Eastside Extension – Tunnel Construction Case History. In Proceedings Rapid Excavation and Tunneling Conference, Edited by M Traylor and J Townsend. Littleton, CO: Society for Mining, Metallurgy and Exploration. pp. 472-494.