The ideal solution for projects requiring mobile operations, accurate weighing of multiple aggregates and powders, including cements and fly ash. The Bison 500 plant from SIMEM can precision mix up to 500 tons per hour in continuous production. Bison 250 will mix up to 250 tons per hour in continuous production.
The main unit of the Bison plant can be ready in just a few hours.
BISON’s main unit contains all that is required to successfully weigh, dose, and continuously mix. The unit includes our MDC continuous twin shaft mixer, 1-2 aggregates, powder and liquid dosing devices, loading belt and SIMEM@tic FLOW Software System to manage precise material charging and continuous mixing for the highest quality product result.
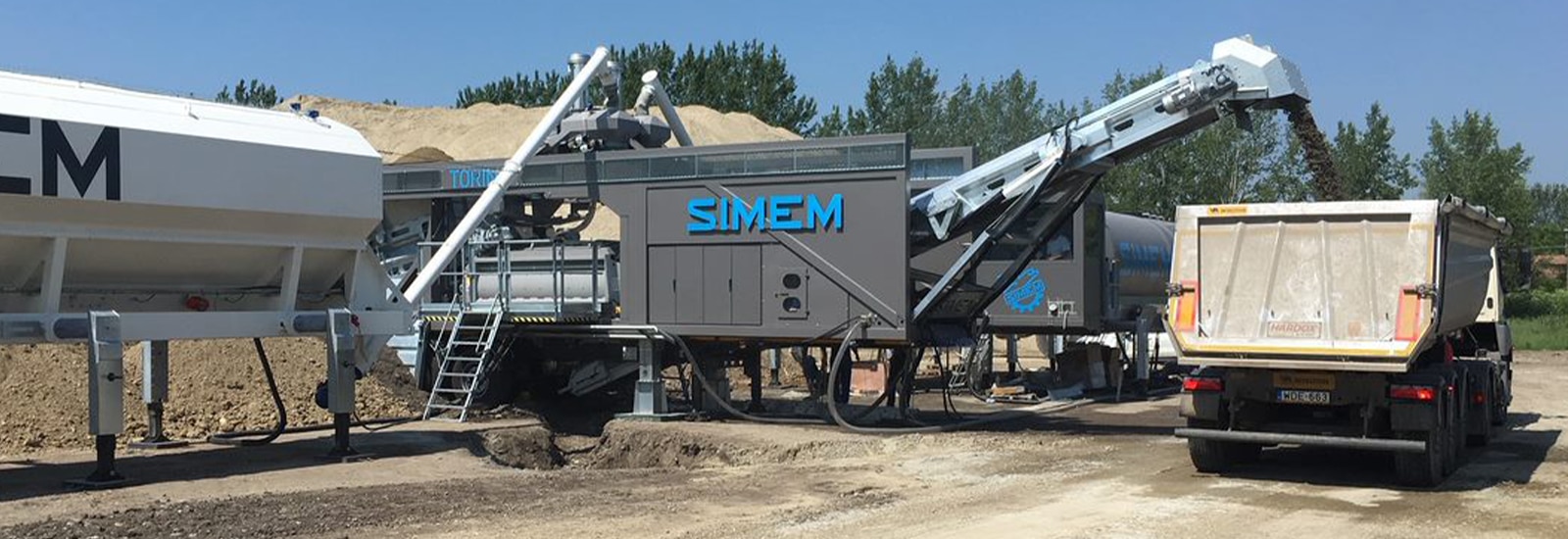
Mobile Mixing Unit
- Trailer Mounted Mixing & Batching Unit
- Hydraulically Powered Plant Set-up – No Cranes Required
- Aggregate Hopper 19.6 cy /15m3 Capacity (divider optional)
- Hot-Dipped Galvanized Steel Structure
- SIMEM@tic FLOW Intuitive Automation
- Weight based Cement & Aggregate Metering System

Continuous Mixing
- Adjustable Mixing Retention Time
- MDC Twin shaft continuous mixer
- Electric Drives
- Bolted Mixing Paddles
- Bolted Mixing Arms
- Adjustable Mixing Arm Configuration
- Practical Wear Liner Replacement
Reliable, Guaranteed Performance
- High Accuracy Metering System
- Independent Cement & Fly Ash Weighing & Metering
- Integrated Water & Admixture Metering
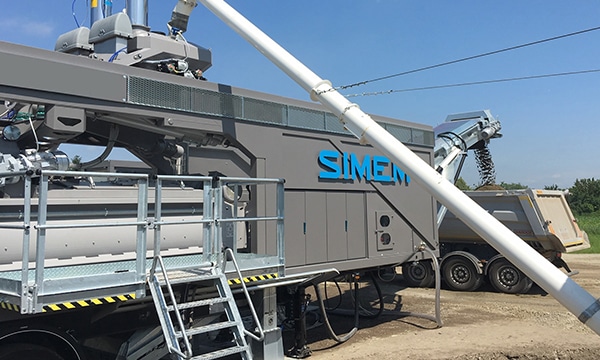
Designed For Capability
Bison is equipped with a MDC continuous twin shaft mixer, storage for up to two aggregates, an aggregate feeding belt, powder and metering devices for water and admixtures.
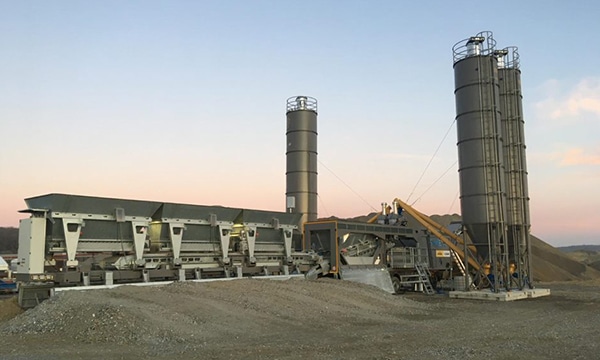
Aggregate Expansion
Aggregate expansion unit transportable with a standard container trailer
- Aggregate extension for 3 additional bins
- Independent aggregate Metering system with load cells for each bin, combined with advanced software control
- Conveyor to Bison
- Hydraulic Operated Galvanized steel panels to contain loading ramps
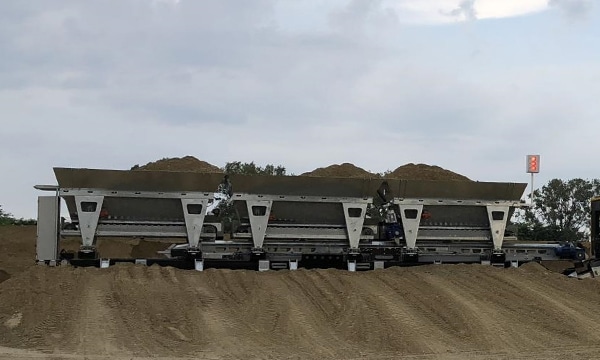
Mobile Cement Silo
Horizontal mobile cement/powder silo transportable with a standard container trailer
- Each horizontal silo includes an integrated hydraulic system to move an attached screw conveyor from transport to production position.
- Vibrators on inclined section and fluidization system with independent air compressor
- Silo capacity ~ 400 bbl (46 m³/1625 cu.ft.)
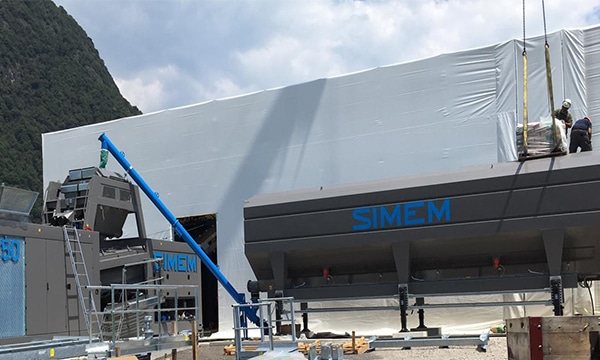
Automation
Simem@tic Flow is an easy to use automation with unbeatable accuracy and flexibility for uninterrupted operation.
- Familiar Windows operating environment with SQL database
- Flexible reporting and backup functionality
- Real time flow correction for each material
- PC/PLC based
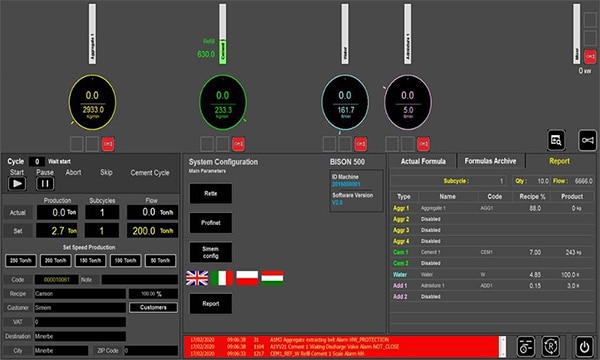
Service Unit
Service unit enhances the mobility of the Bison package with all the infrastructure components needed for a quick setup installed on a frame that be transported with container trailers.
- Diesel driven generator with the capacity to operate the Bison and all optional units
- One 5,300 gallon (20,000 liter) water tank
- Two admixture tanks, each with a capacity of 530 gallon (2,000 liter)
- Air compressor – screw type with air dryer and tank
- Insulated control room
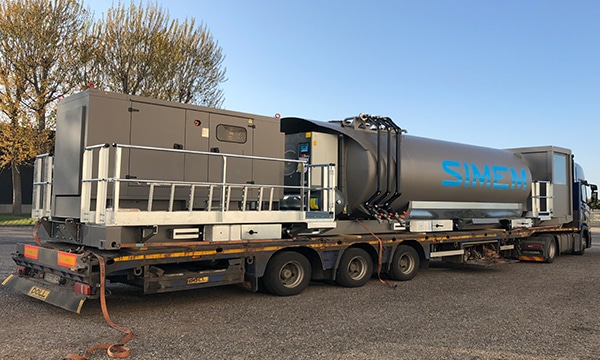
Specifications
MODEL | 250 | 500 |
Aggregate bins (max) | 4 | 4 |
Mixer – Continuous Twin Shaft | MDC 200 | MDC 500 |
Capacity (tons/hr) | 250 | 500 |